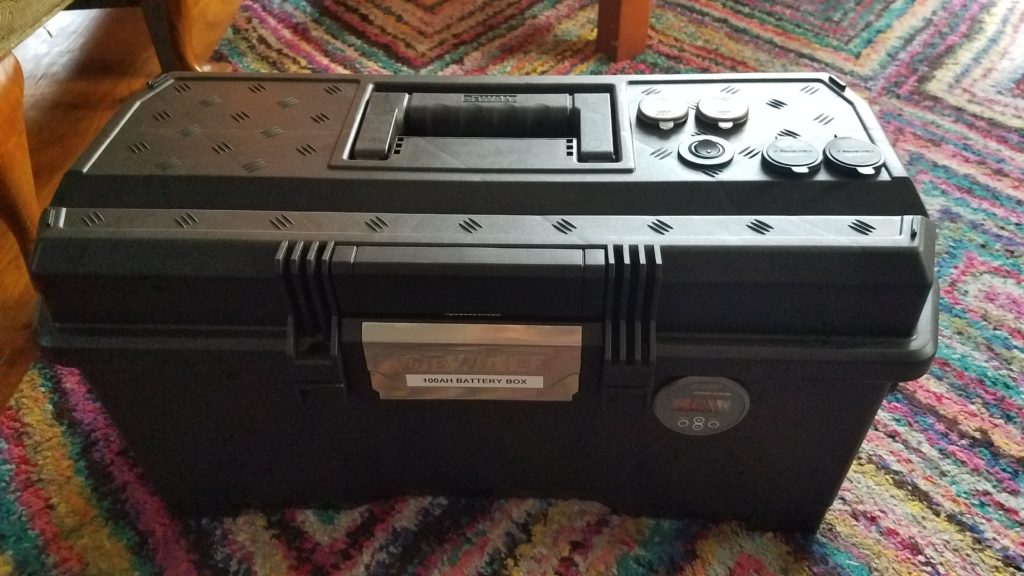
Ok, so this is a big one. I wanted to build a battery box that could keep me going a few days without being able to charge while camping and/or operating. I also wanted accurate power accounting and the ability to understand my power consumption and have alarms when usage exceeds specified thresholds, providing the opportunity to either adjust usage or in an emergency not be surprised when I drop out. I also wanted to design the system for maximum flexibility when it comes to charging and connecting loads. Most commercially-available systems that met capacity and power needs were designed around inverters and larger 30+ volt solar panels that were designed to mount on structures or large vehicles like RVs or vans rather than the smaller and more portable 18v open circuit foldable panels that are used more commonly for my purposes. Having a wider range of panels that I can use is better because it would be good to charge from either so not building in charging was ideal. I also found the options for high-amperage DC connectors lacking in many pre-built options. Some units would have one or two 25A outputs, but those are at the max current range some of my radios will draw at full power. I wanted some breathing room current-wise. In the event I wanted to operate one of my bigger radios at full power I’d rather not risk burning a fuse out or damaging my power source – especially in the field while I’m relying on it. It’s also nice to have many connectors available on the source which eliminates the need for a bunch of splitters. None of the commercially-available options I evaluated provided more than two high amperage connectors. Finally, I wanted a couple USB fast chargers for my and my partner’s devices which many commercial options provided, but they’d typically provide a single fast charging port.
I took some inspiration from a Powerwerx box that a fellow ham and NET team member Laura, KI7ZZQ purchased. That battery box was designed to accommodate a 50-70Ah battery which wouldn’t physically fit any of the 100Ah batteries I had been considering during the design phase, but it provided me a rough template I could build from in terms of layout. As with that box just including power distribution and monitoring in the box was a way I could reuse existing systems I have that perform well without having to buy more of those components. Buying a bunch of new parts is pretty expensive so not including more core devices in the box is definitely a plus.
This was not a cheap project, but I think it’ll be worth it.
Theory and design
By selecting a 100Ah battery I get 80Ah of usable power from the system without significantly decreasing the battery’s lifecycle. Using LiFePO4 batteries instead of lead-acid means I get an additional 30% depth of discharge without the destructive effects of discharging to 50%… The LiFePO4 battery I selected also weighs 26lbs. A similar capacity lead acid battery would weigh a lot more and probably require a much sturdier and expensive enclosure. Another advantage of LiFePO4 batteries is the lack of battery memory – that is to say the useful lifetime of a battery isn’t diminished by leaving it in a partially-charged state. Some battery technologies suffer from that problem which is a problem if you’re in a situation where you might not be able to completely recharge the battery completely during use. As far as parts go I wanted to attempt to source the parts I didn’t already have from a variety of vendors… I had a preference for smaller and more local vendors, but that didn’t work out 100% of the time. The enclosure (tool box) and a 1 1/8″ hole saw are two examples of where that didn’t work. The bill of materials will list the source of each component.
So let’s start with the system design itself. There are a few core components that I knew I’d probably want from designing a bigger high amperage system when my partner were considering purchasing and building out a van for camping/touring. The core parts that everything else would be designed around are:
- 100Ah LiFePO4 battery
- Reliable battery state and power usage monitoring capability
- Battery disconnect for safety and preventing parasitic loads from draining the battery
- Circuit breaker for the battery to prevent damage to components or fires
- DC subpanel to split out and protect branch circuits
- Two switched USB rapid chargers.
- Flexible charging – AC-to-DC chargers (wall socket, generator), solar panels of various types, and DC-to-DC (vehicle, independent DC power supply, DC generator outputs)
Those components are roughly connected and arranged as follows. Chargers can be connected to any of the powerpole connectors listed below, and so can loads. The only loads that wouldn’t be connected to powerpole connectors are devices directly connected to the built-in USB A/C rapid chargers. You’ll notice there’s a power line running from the battery to the 500A shunt resistor and power supply that feeds the Victron BMV-712 through a 100mA fuse, bypassing the circuit breaker which also doubles as a battery disconnect. That’s intentional as the BMV-712 requires constant power to track battery state and if powered off it will lose its zero-point configuration. This is the only parasitic load that isn’t switched in this system apart from the BMS built into the battery, but it’s required to get accurate battery status so I compromised.
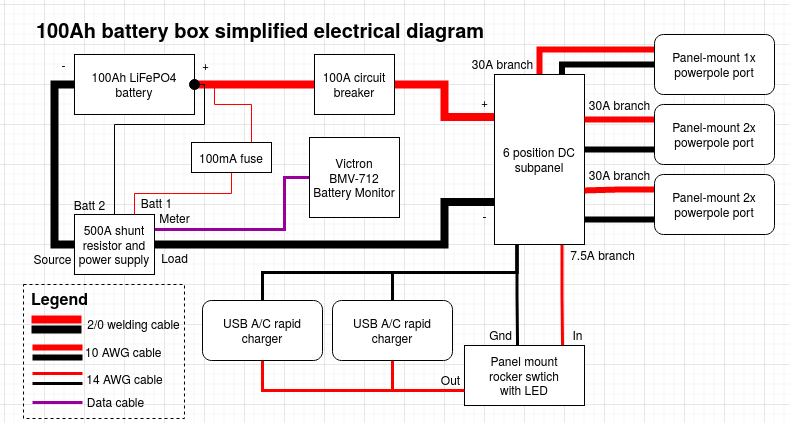
Materials / parts
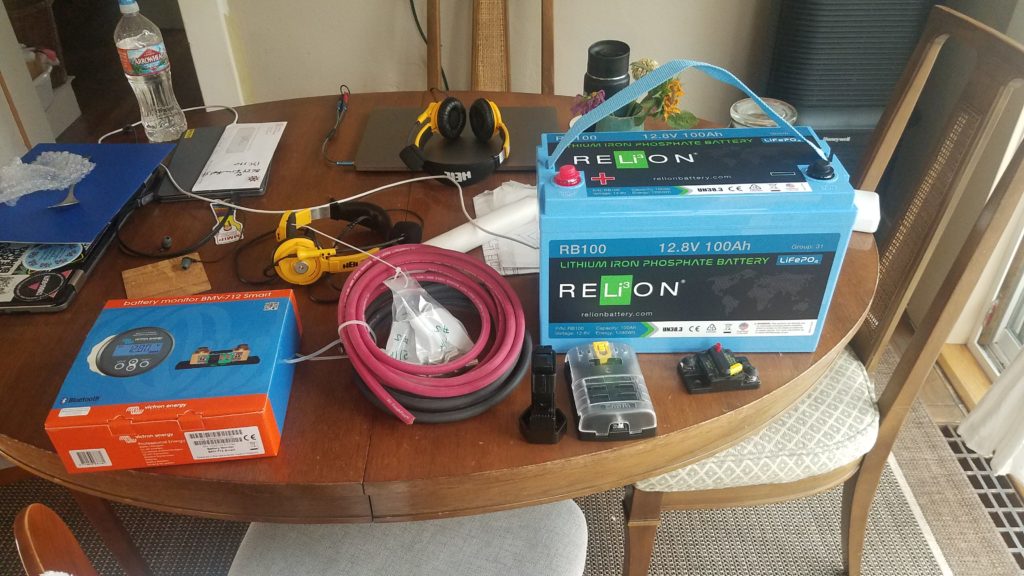
Description | Qty | Make and model | Vendor | Link | Notes | Tool? |
---|---|---|---|---|---|---|
100Ah LiFePO4 battery | 1 | Relion RB100 | LightHarvest Solar | Here | N | |
Red #2/0 welding cable, 10′ | 1 | ? | — | Here | N | |
Black #2/0 welding cable, 10′ | 1 | ? | — | — | N | |
100 amp circuit breaker ***** | 1 | Eaton 285100F | — | Here | N | |
6-position 100A DC subpanel | 1 | BlueSea 5025 | — | Here | N | |
Hammer-type crimping tool | 1 | TE(?) | — | Here | Y | |
Battery monitor | 1 | Victron Energy BMV-712 | — | Here | N | |
#2/0 Lug Ring Terminal (5/16″) * | 3 | ? | — | Here | N | |
#2/0 Lug Ring Terminal (3/8″) * | 3 | ? | — | — | N | |
#2/0 Lug Ring Terminal (1/4″) * | 5 | ? | — | — | N | |
10A LiFePO4 14.6v battery charger | 1 | Bioenno Power BPC-1510A | Bioenno Power | Here | Dedicated AC-to-DC charger | N |
Tool box | 1 | Dewalt DWST24082 One Touch Tool Box, Black | Home Depot | Here | Used as enclosure | N |
#10-24 3/4″ cap screws and nuts (x8?) | 1 | ? | — | Here | N | |
#10-24 1″ cap screws and nuts (x6?) | 1 | ? | — | Here | N | |
#10-24 Bonded neoprene washer (x4) | 3 | ? | — | Here | N | |
1 1/8″ hole saw | 1 | ? | — | Here | Used for Powerwerx panel mount devices | Y |
Panel mount powerpole socket (x2) | 2 | Powerwerx PanelPole2 | Powerwerx | Here | N | |
Panel mount powerpole socket (x1) | 1 | Powerwerx PanelPole1 | — | Here | N | |
USB A QC + USB C PD charger, panel mount | 2 | Powerwerx PanelQCUSBC | — | Here | N | |
Bonded 10GA stranded copper wire, 25′ | 1 | Powerwerx Wire-RB-10-25 | — | Here | Used for 30A branch circuits | N |
Bonded 14GA stranded copper wire, 25′ | 1 | Powerwerx Wire-RB-14-25 | — | — | Used for 15A branch circuit | N |
Powerpole to “cigarette lighter” adapter | 1 | Powerwerx SOC-PP | — | Here | Stored in the enclosure as an adapter | N |
4-Way powerpole splitter | 2 | West Mountain Radio PWRNode | Ham Radio Outlet | Here | Used as splitters for the 2x panel mount powerpole sockets | N |
Panel mount rocker switch w/red LED, 15A max | 1 | Powerwerx PanelSW-Red | — | Here | N | |
15/30/45A red powerpole housings | 6 | Powerwerx PowerpoleCase | — | Here | N | |
15/30/45A black powerpole housings | 6 | — | — | — | N | |
Powerpole retention clips | 6 | — | — | — | N | |
45A powerpole contacts | 22 | — | — | — | N | |
Powerpole crimper | 1 | Powerwerx TRICrimp | — | Here | Y | |
F2 blade connectors, 12-10GA | 3 | ? | ? | ? | N | |
F2 blade connectors, 16-14GA | 4 | ? | ? | ? | N | |
Lug ring terminal, 12-10GA | 6 | ? | ? | ? | N | |
Lug ring terminal, 16-14GA | 2 | ? | ? | ? | N | |
7.5A ATC blade fuse * | 3 | ? | ? | ? | N | |
30A ATC blade fuse * | 5 | ? | ? | ? | N | |
Assorted ATC blade fuses | 6 | ? | ? | ? | Included in enclosure | N |
Packing foam ** | ? | ? | ? | ? | N | |
Electrical tape *** | 1 | ? | ? | ? | N | |
1 1/4″ bolt and flange nut **** | 1 | ? | ? | ? | N | |
Zip ties | 5 | ? | ? | ? | N | |
3/16″ (?) drill bit | 1 | ? | ? | ? | Used to drill holes in plastic fins in toolbox for zip ties | N |
Electric drill | 1 | ? | ? | ? | Used w/hole saws and drill bits | Y |
2″ hole saw | 1 | ? | ? | ? | Used to drill a hole for the Victron BMV-712 panel | Y |
Phillips screw driver | 1 | ? | ? | ? | Y | |
Metal shears | 1 | ? | ? | ? | Used to cut #2/0 welding cable | Y |
Diagonal cutters | 1 | ? | ? | ? | Y | |
Socket wrench | 1 | ? | ? | ? | Y | |
?mm socket | 1 | ? | ? | ? | Used for shunt bolts | Y |
?mm socket | 1 | ? | ? | ? | Used for battery terminal bolts | Y |
?mm socket | 1 | ? | ? | ? | Used for #10 nuts | Y |
?mm socket | 1 | ? | ? | ? | Used for DC subpanel 100A contacts | |
Needle nose pliers | 1 | ? | ? | ? | Used to help pull wires, tighten panel mount nuts | Y |
Claw hammer | 1 | ? | ? | ? | Used w/ the TE hammer-type crimping tool | Y |
Pocket knife ****** | 1 | ? | ? | ? | Y |
Legend
? Can’t remember/unknown
— Same as above
* Includes spare(s) or extra(s)
** This is small-cell plastic foam used as packing to keep the battery from moving around a lot
*** Used mostly to bind wires and as extra insulation on the #2/0 ring terminals. Also used to physically shore connections up due to gaps in wire jacketing or potential stress points from bends.
**** Used as insurance to hold the toolbox closed in case the latch is opened unintentionally
***** Doubles as a battery disconnect switch
****** Used to clean plastic burrs left from the hole saws and to cut the jacketing on the #2/0 cable in preparation for crimping
Assembly
This was done in a a couple phases – in part because I was waiting for things to come in the mail, and in part because I sort of “winged it” building this out in terms of mounting components to the enclosure. The first thing I did was pick locations for each of the high amperage components: the battery, BMV-712’s 500A shunt, 100A circuit breaker, and the DC subpanel. I made sure to allow for enough space to run cables to and from each component before drilling holes for them. The battery was pushed to the left side of the tool box. This makes it a bit awkward to carry but creates enough space in the right side to mount everything.
Once I found a good placement for the components that required mounting I just drilled holes in the enclosure using the components as a template. For each component I drilled an initial hole and inserted one of the #10-24 cap screws in the hole to hold it. I then drilled out a second mount and placed another bolt in it. After I’d placed all the components and got the holes drilled for them I added the #10 bonded washers with the neoprene side on the outside of the enclosure. To minimize jagged edges from threads on the outside of the enclosure I put the phillips end of the cap screws on the outside as well. The nuts and lock washers were placed on the inside.
The next step was to route, measure, and cut the high amperage #2/0 welding cable between each component. I did a dry run of the cable from component to component and cut each piece to length. I ran a piece of from the negative battery post bolt to the BMV-712 shunt battery terminal, cut it, ran another piece from the shunt to the negative terminal of the DC subpanel to the BMV-712 shunt load terminal, and cut it. I then took the red #2/0 welding cable and ran it from the positive terminal on the DC subpanel to the 100A circuit breaker, cut it, and then ran another piece from the circuit breaker to the positive battery terminal, and then cut it.
For each piece of #2/0 welding cable I cut I stripped enough jacketing off of the end to fix the appropriate #2/0 lug ring terminal to the wire. Make sure the hole on each lug ring terminal matches the post you’re planning to connect it to. It’s worth double-checking before you crimp since each section of wire is cut to length. After verifying that I was using the right ring terminal for each connection I crimped them to the #2/0 welding cable. I then wrapped the bare metal parts of the lugs that might be prone to shorting with electrical tape since I didn’t have any heat shrink tubing. I also used the tape to shore the joint between the jacketing of the welding cable and crimp-on connector.
The next step is to hook the high amperage wire up to each component. This will help us figure out where to run the legs from the DC subpanel and to help us properly place the panel mount components without interfering with the high amperage wire runs and components mounted inside the enclosure. Before making the connections between components verify the polarity of the connections and break the circuit by pressing the reset button on the circuit breaker. The connections should be made according the the simplified wiring diagram above.

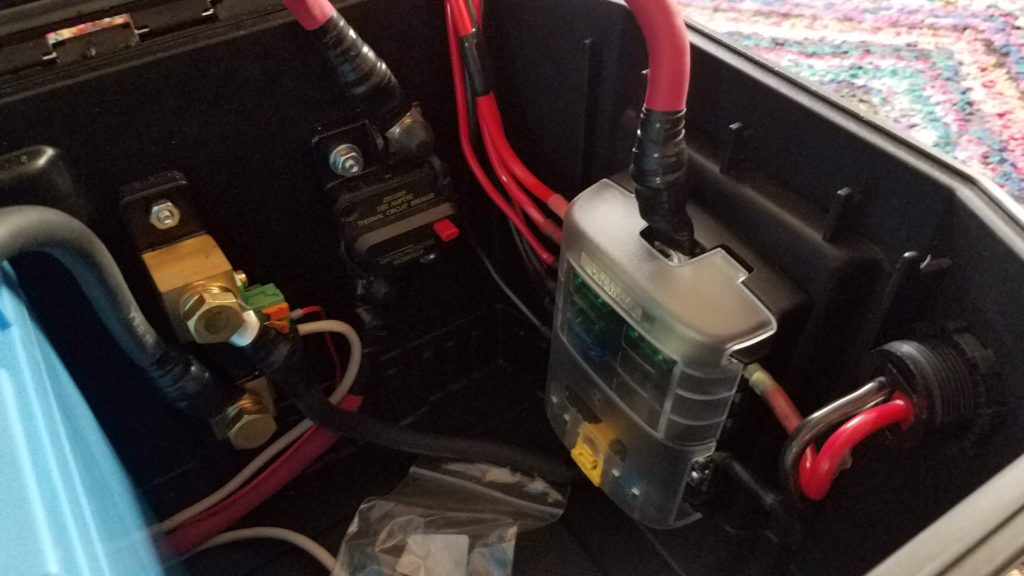
The next step is to place and mark each panel mount component. I chose to mount the BMV-712’s meter on the front of the tool box to the right of the latch since I mounted the DC subpanel on the flat part of right end of the toolbox. I mounted the 1x powerpole panel mount component on one of the angled surfaces on the right end of the enclosure so I could connect a charger easily when it’s stored on a shelf. I picked spots for the panel mount components on the lid because I think that’s going to be the easiest spot to make connections in the field. All the panel mount components were placed in such a way that the panel mount nuts cleared the plastic “fins” on the inside of the enclosure. Special care should be taken when placing components in the lid. There are a lot of plastic fins on the inside of the lid. Use the 2″ hole saw to cut the hole for the Victron BMV-712’s meter, and for all the other Powerwerx panel mount components use the 1 1/8″ hole saw. You might need to shave the decorative raised lines on the lid down with a pocket knife to ensure that the panel mount components mate to the outside of the lid properly.
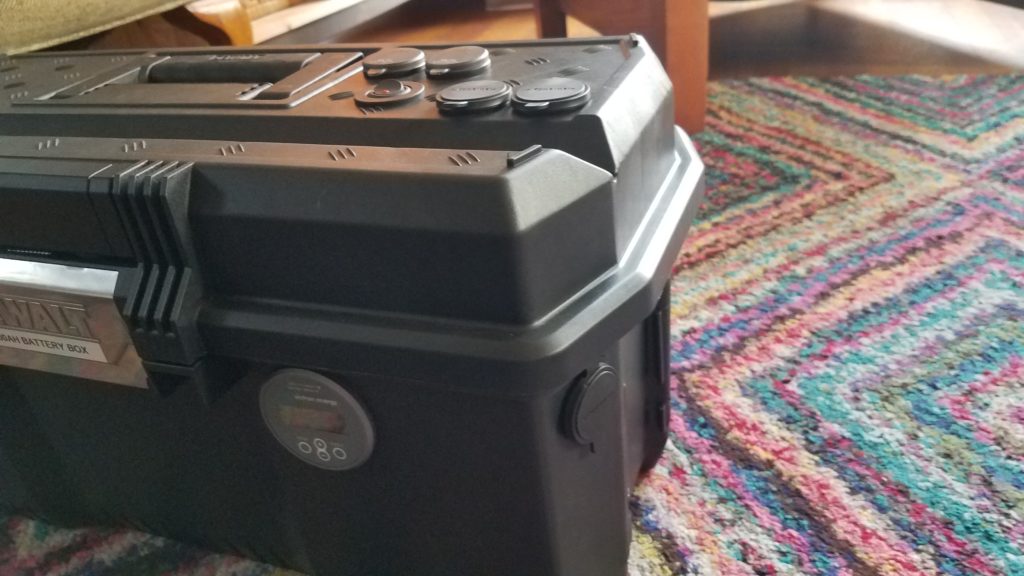
At this point it’s time to start making the connections from the subpanel to the panel mount powerpole connectors. Since I used 10GA wire capable of handling 30A it’s hard to daisy chain between ports so I opted to use some PWRNode splitters to make the connections to the 2x panel mount powerpole sockets. I made some shorter 2″ stubs of 10GA wire and crimped 45A powerpole conductors on both ends of each stub. Connecting all 4 ports requires 8 2″ stubs. Once I crimped the 45A conductors on I added the powerpole housings to one side of each stub. The other side of the stub was inserted into the panel mount connector. Each panel mount socket is connected to a single run of cable from the DC subpanel with powerpole connectors on the end of it. The idea is that each socket can support up to 30A of total current draw. Once that was complete the side with the housings were connected to the PWRNodes and powerpole retention clips were installed to keep all the powerpole connectors in place. The 1x powerpole connector was run directly to the DC subpanel. Each leg was then fused in the DC subpanel with a 30A fuse. I used some electrical tape to support the “joints” between the powerpole connectors that lead to the DC subpanel and the powerpole connectors themselves.
The next step in wiring the system is to connect the panel mount chargers in parallel and switch them with the rocker switch using the 14GA wire. This is accomplished using the connections as detailed in the simplified electrical diagram. The brass connector on the switch connects to the ground, the middle connector connects to the DC subpanel, and the silver connection on the end connects to the USB chargers wired in parallel. The photo below details how the connections to the panel mounted devices and sockets. I drilled a hole in one of the fins on the lid of the toolbox and wire tied the wires coming from the DC subpanel to the lid to keep the wires from migrating a lot during transport. I also used wire ties to hold some of the wires together coming out of the individual parts.
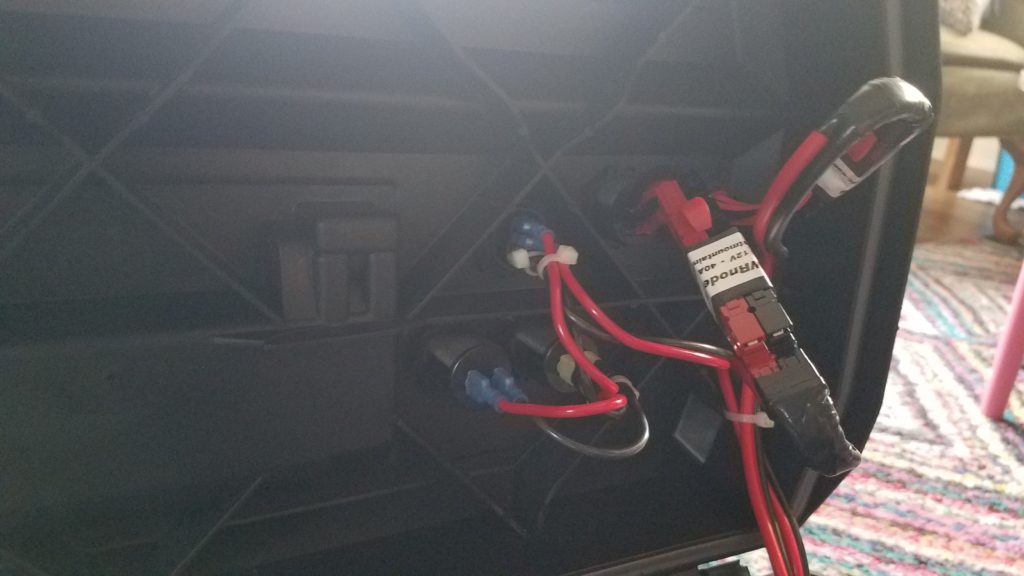
Now that all those connections are complete we can re-connect the battery, and while we’re at that we’ll hook the BMV-712 up. The BMV-712’s box has a handy connection diagram. In this step we’ll connect the battery and the BMV-712. First connect the BMV-712’s red (positive) wire connected to the temperature sensor lug to the battery using the ring terminal along with the terminal on the #2/0 welding cable. Both should connect directly to the positive battery terminal. Take care not to short the pin end of the BMV-712’s red power cable while connecting it. Once that’s connected to the positive battery terminal connect it to the B1 pin on the BMV-712’s shunt, and connect the black temperature monitor cable to B2 on the BMV-712’s shunt. The BMV-712’s manual will detail how that connection should be made. Now connect the gray 6-pin modular data cable from the shunt to the BMV-712’s panel mount meter. Once that’s been hooked up you can connect the negative battery terminal to the black wire leading to the battery side of the BMV-712 shunt. When properly connected the panel should light up blue and the display should become active. [Note: this was updated to include directions to connect a BMV-712 temperature sensor.]
Once all these connections are made and the battery is re-installed make sure you install a 7.5A fuse in the subpanel on the leg that connects to the USB chargers. If the 7.5A fuse blows during testing one or both of the USB chargers are wired backward. Use the + and – on the bottom to properly wire the positive and negative sides of the charger. Install 30A fuses on each leg that leads to powerpole panel mount sockets.
Now we’ll pull the yellow reset bar on the breaker back in to energize the DC subpanel. Once the subpanel is energized we can test the USB charger leg of the circuit by activating the toggle switch. The red LED should activate on the toggle switch, and both USB chargers should show their voltage with blue numerical LED displays. If all three of those work that’s wired correctly.
As a bonus I added some scraps of plastic closed cell packing “foam” around the battery to dampen vibration and shock to help hold the battery in place.
The installation is complete we can move onto programming the Victron BMV-712.
Configuring the Victron BMV-712
At this point we should set up the battery monitor. Some of the instructions in this section come in part from instructions provided to me by LightHarvest Solar. I modified some of the values in the configuration to better fit my use-case. The instructions in this section assume you’ve charged the battery completely using an appropriate LiFePO4 battery charger. I used the Bioenno charger listed in the bill of materials to fully charge the battery before configuring the BMV-712. To begin you’ll want to install the VictronConnect app on a device that it supports which also has Bluetooth. There are versions for IOS and Android.
After opening the app you’ll want to select your BMV-712 and pair with it. I also recommend changing the BMV-712’s pin to make sure someone doesn’t pair with it and modify its settings, especially if you’re around RVs or others with a Victron battery monitor. You can then modify the settings on the device. The major configuration tasks to do are configuring the parameters for your battery and doing a zero-point reset once your battery has been fully charged. To begin with we’ll configure the battery monitor with the properties of the Relion RB100. You can leave all the settings as defaults unless they’re specified below. I got the initial values and instructions to configure the battery monitor from LightHarvest Solar. It was provided with the purchase of the BMV-712. After opening settings and choosing “Battery” set the following:
- Battery capacity: 100Ah (this is a 100Ah battery)
- Charged voltage: 13.9V
- Discharge floor: 20% (This is the lowest capacity you want the battery at)
- Peukert exponent: 1.00
- Charge efficiency factor: 99%
- Current threshold: 0.10A
- Time-to-go averaging period
Optionally, you can configure alarms for the system. I turned on the alarm buzzer and set the “Low SOC alarm” to go off at 40% and clear at 45%. Since you don’t want to draw the battery down lower than 20% I picked 40% to give me a warning well before I draw it down. If you draw the battery down below the discharge floor it can be damaged. You can also optionally configure a temperature alarm if you have the BMV-712 battery temperature sensor. See the “updates” section at the bottom of this post for details.
Once the battery has been configured and ALL loads and chargers except the BMV-712 have been disconnected you can then click the “synchronize” button, and then click “calibration”. Synchronize sets the battery state-of-charge to 100%. Calibration zeroes out the current measurement on the shunt resistor. If you disconnect the battery monitor you’ll need to redo this part of the process starting with a full charge.
Using the BMV-712
While this post is mostly focused on the app the display panel on the BMV-712 can display the status information using the arrow keys on the front panel. Navigating that is pretty easy, but I’d also recommend reading the manual as there’s more to the panel than just displaying data. The most common screens I use in the app are the device list which is used to manage Victron devices. They have an entire ecosystem of devices that can be managed and monitored from this app. I go through this to connect to my battery box. The battery box has been renamed in the settings (gear icon seen in the other screens). The status page shows you all the current stats for your battery – state of charge, voltage levels, current, and power. There’s one thing that’s cut off at the bottom which is the status of the control panel’s relays. For my configuration the relay is open since it’s not really doing anything. The history tab shows you stats for your battery over time. This data can be cleared, but it’s nice to understand what you’ve done with your battery over time so I probably won’t be clearing that until I replace the battery in the system. The trends tab is really nice to use when you’re watching your battery in real time from within the app. You don’t get data points when your app isn’t connected unless you get a Victron Cerbro GX or similar device but that’s overkill for my use-case.
Problems left to solve
There are still some problems to solve. I need to install some sort of barrier that prevents the battery from moving to the right inside the enclosure. I’m thinking about bolting a barrier into the enclosure to prevent too much movement. The toggle switch on the top isn’t weather resistant either. The toggle switch comes with a plastic cover but it’s impossible to install without the rocker switch popping out of the panel mount.
Updates
I decided to add a temperature sensor to the BMV-712 in order to make sure I’d get an alarm if the battery was out of the appropriate range to charge which is a more narrow range than the discharging temperature. The changes I made to connect the battery temperature sensor was to purchase a temperature sensor for $25. I disconnected the old wire running from the positive battery terminal to the current shunt, connected the new one, and connected the new larger lug to the battery terminal. I then connected the black wire for the temperature sensor to the open input on the shunt. After that I configured the BMV-712 to use the second input as a temperature sensor using the web application. Then I configured my high temperature trip temp to 55C and the high temperature clear to 53C. The alarm will go off 5C before the battery’s charge limit of 60C. The low temperature alarm was set to -15C and the low temperature clear was set to -13C. -15C is 5C above the battery’s minimum charging temperature limit of -20C. The connection diagram has been updated to reflect the new temperature sensor connection. This post talks about recently implemented changes to the battery box.